roughing end mill depth of cut
This is because the cutting resistance is reduced because the chips are broken into short lengths by the wavy cutting edges. Cutting speeds also vary with the end mill type - roughing end mills can go.
The Anatomy Of An End Mill In The Loupe
Running program the other day and i notice broken 58 dia roughing HSS end mill.
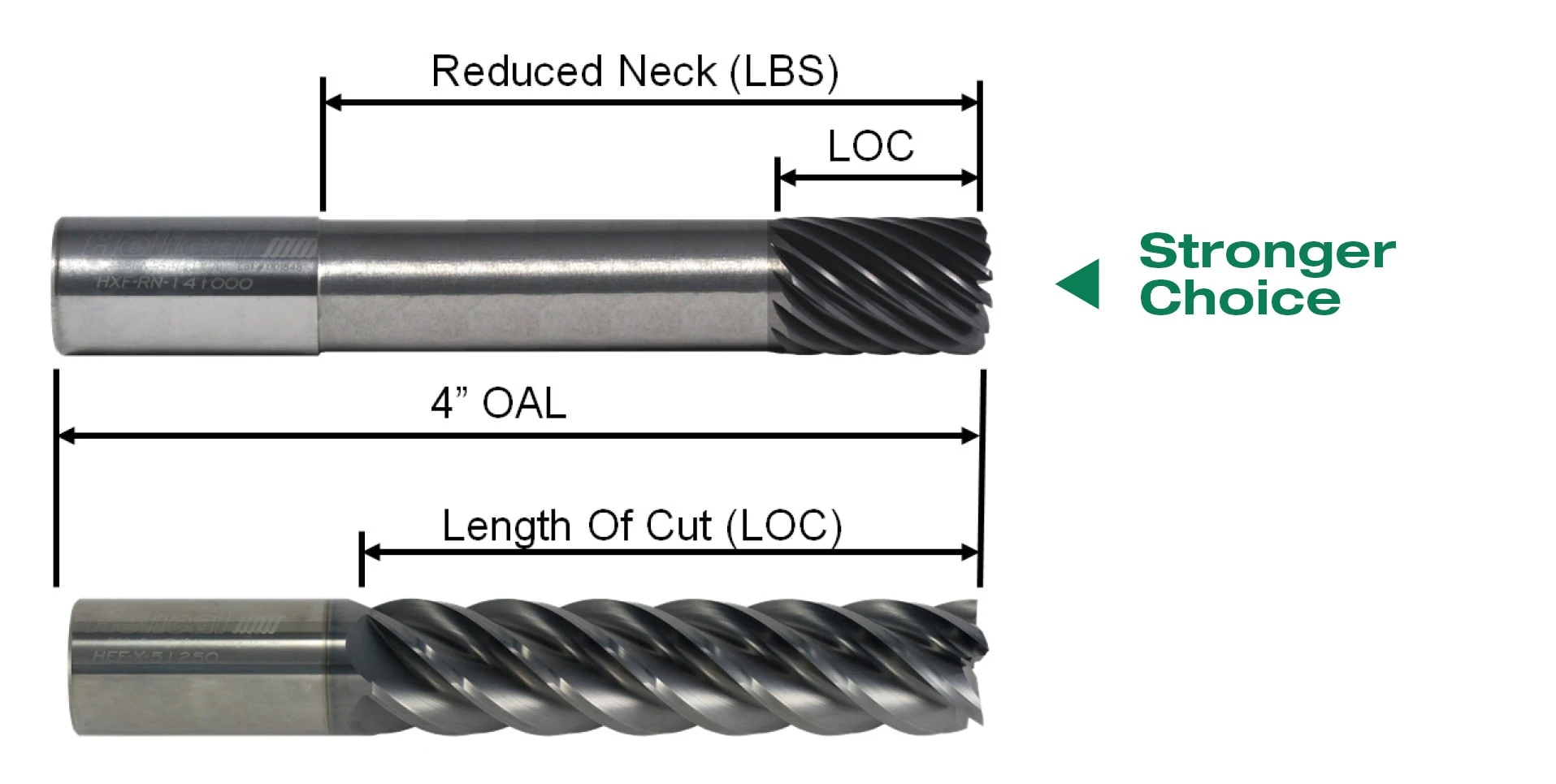
. Ad For Taps Dies Cutting and Measuring Tools. The tooth design and flute construction minimizes deflection and maximizes chip ejection. While traditional roughing is occasionally necessary or optimal it is generally inferior to High Efficiency Milling HEMHEM is a roughing technique that uses a lower Radial Depth of Cut RDOC and a higher Axial Depth of Cut ADOC.
For high-speed roughing width of cut is usually set at somewhere between 5 and 10 percent of the cutting tool diameter. Multi-flute end mills create better surface finishes due to a lighter chipload - per flute. This setting will impact RCT calculations as well.
This means a 050-inch end mill will be engaged 0025 to 0050 inch. Cobalt roughing end mills are designed to withstand heat and abrasion and can be run at higher production rates without sacrificing tool life. Side loading is dramatically reduced with lower helix angles making it easier to mill thin walls.
I replaced end mill and rerun and see end mill goes in a drilled hole 125 deep and feeds to 2nd hole a inch away at 20 ipm feed which i slow to 15 ipm feed so end mill does not break again. WIDIA HANITA 5329387 Series Eccentric Rougher 6 Flute Inch Roughing Finishing End Mill 508 mm Max Depth of Cut 3175 mm Dia Shank Part. Two flute end mills are center cutting where multi-flute end mills can vary.
Milling Legend v c Cutting speed mmin n Spindle speed revmin v f Feed speed mmmin a p Axial depth of cut mm a e Radial depth of cut mm f Feed per rev mmrev z Number of teeth f z Feed per tooth mmtooth D Cutter diameter mm h m Average chip thickness mm Q Material removal rate cm3min Drilling Legend. Deep axial cuts require the use of chipbreakers notched cutting edges that prevent chips from wrapping around end mills or part features and causing damage to either or both. They are designed to remove large amounts of material quickly and more efficiently than standard end mills.
Ball end mills also known as ball nose end mills are used for milling contoured surfaces slotting and pocketing. Inch and Metric Mills - Single or Double End Roughing Mini Long Ball End. Max depth of cut slotting with roughing end mills.
Due to variable spacing of flutes combined with the NR roughing profile vibrations cutting forces are minimized and metal removal rates are maximized. Also for the same reason the depth of cut for semi-finishing end mills can be increased. The cutting speed varies with the amount of radial depth of cut when profiling and axial depth of cut when slotting.
This results in lower cutting pressures at a given radial depth of cut. Roughing end mills also known as hog mills are used to quickly remove large amounts of material during heavier operations. A ball end mill is constructed of a round cutting edge and used in the machining of dies and molds.
This spreads wear evenly across the cutting edge dissipates heat and reduces the chance of tool failure. Volumes of material can. Radial Side Depth of Cut.
Beyond that point axial cutting pressures cause end mill deflection and hamper good chip formation. A rule of thumb Ive been told for end mills is max depth is about 12 the cutter dia but its only a rule of thumb. Roughing End Mills have scallops on the cutting edges which cause the chips to break into smaller segments.
Like Ken says many variables on what force the cutter experiences biggies being material feed rate rigidity of machine rigidity of set up etc. Vibration dampening variable flute spacing 45 high helix flute design Stabilizing cutting edge geometry PVD applied. Stock Material Surface Speed.
Multi-Cut end mills are specifically designed for high-performance roughing operations. Cut Depth 05mm Pf04mm. The deeper you go the slower you need to go.
Made of solid carbide these end mills are harder stronger and more wear resistant than high-speed steel and cobalt steel for the longest life and best finish on hard material. End mill diameter should measure half the cutting length depth of cut. Standard depths of cuts for roughing end mills can be set at a larger value than ordinary type end mills.
End Mill Speed Feed Calculator. Their extreme hardness means they are brittle so a highly rigid setup such as a CNC machine is necessary to prevent the end mill from breaking. This will adjust the feedrate if less than the tool rad.
End Mill Terms A - Mill Size or Cutting Diameter B - Shank Diameter C - Length of Cut or Flute Length. ROUGHING END MILLS Roughing cuts are generally for preparing the surface. Multifunctional End Mill for High Speed Roughing and Precise Side Milling Work Materials.
End Mill An Overview Sciencedirect Topics
The Anatomy Of An End Mill In The Loupe
Check Out Our New 6 Flute Endmill End Mill Milling Machine Cnc Programming
What To Know When Selecting An End Mill End Mill The Selection Machining Process
Basic End Mills Technical Information Msc Industrial Supply Co
The Anatomy Of An End Mill In The Loupe
Endmill Selection Guide Redline Tools Redline Tools
End Mill Tool With High And Low Helical Flutes And Related Method For Rough Cutting And Finishing A Workpiece Destiny Tool